Aerospace Casting: Techniques, Advancements, and Applications
Aerospace casting is a crucial process in the manufacturing of aircraft components. Investment casting is a widely used method in aerospace casting, which involves pouring molten metal into a mold to create a part. The aerospace industry demands high-quality and durable components that can withstand extreme conditions, and investment casting is one of the best methods to produce such parts.
Precision investment casting is a process that allows for the creation of complex geometries with tight tolerances. It is ideal for producing aerospace components such as actuator components, cargo systems, and bearing cages. The process involves creating a wax pattern of the desired part, coating it with a ceramic shell, and then pouring molten metal into the shell. Precision investment casting can produce parts with a surface finish of up to 125 RMS, making it suitable for applications that require a smooth surface.
In addition to precision investment casting, aerospace casting also involves other processes such as heat treating, coating, and CNC machining. Non-destructive testing (NDT) is also an essential part of aerospace casting to ensure the quality of the parts. NDT testing methods such as X-ray, ultrasonic, and magnetic particle inspection are used to detect any defects in the parts. Aerospace casting companies such as Barron Industries have achieved NADCAP certification for their investment casting capabilities, ensuring that their parts meet the stringent standards set by the aerospace industry.
Overview of Aerospace Casting
Aerospace casting is a manufacturing process that involves pouring molten metal into a mold to create a specific shape. This process is used to create complex parts that are used in aerospace applications. The aerospace industry requires high-quality parts that are lightweight, durable, and able to withstand extreme conditions.
Investment casting is a common type of casting used in the aerospace industry. It is a process that involves creating a wax pattern of the desired part, coating the pattern in ceramic, and then melting the wax out of the ceramic shell. The resulting shell is then filled with molten metal to create the final part. Investment casting is capable of producing complex parts with tight tolerances and a high degree of accuracy.
Aerospace alloys are specially formulated to meet the demands of the industry. These alloys are designed to be lightweight, strong, and resistant to corrosion and high temperatures. Common alloys used in aerospace casting include titanium, aluminum, and nickel-based alloys.
The aerospace industry relies heavily on casting to produce a wide variety of parts, including engine components, structural parts, and landing gear. Casting allows for the creation of parts with complex geometries that would be difficult or impossible to create using other manufacturing methods.
In conclusion, aerospace casting is a critical process in the manufacturing of parts for the aerospace industry. Investment casting and the use of specialized alloys are key components of this process. The ability to create complex parts with tight tolerances and high accuracy makes casting an essential part of aerospace manufacturing.

Types of Aerospace Castings
Aerospace castings are an important component of the aerospace industry. They are used in the construction of aircraft engines, landing gear, and other parts. There are several types of aerospace castings, each with its own unique characteristics and applications.
Investment Castings
Investment casting, also known as precision investment casting, is a casting process that is used to create parts with complex geometries and fine surface finishes. This process involves creating a wax pattern of the part, coating the pattern with a ceramic material, and then melting the wax out of the mold. The mold is then filled with molten metal, which solidifies and is removed from the mold. Investment casting is known for its ability to produce parts with tight tolerances and complex geometries. It is also a popular choice for rapid prototyping.
Sand Castings
Sand casting is a casting process that uses sand as the mold material. This process involves creating a pattern of the part, placing the pattern in sand, and then removing the pattern to leave a cavity in the sand. Molten metal is then poured into the cavity, which solidifies and is removed from the sand mold. Sand casting is a versatile process that can be used with a variety of ferrous and non-ferrous alloys. It is also known for its ability to produce large parts with relatively low tooling costs.
Permanent Mold Castings
Permanent mold casting is a casting process that uses a reusable mold to create parts. This process involves pouring molten metal into a mold, which is made of steel or another material. The mold is designed to be reusable, which makes it a cost-effective option for high-volume production. Permanent mold casting is commonly used with aluminum alloys, ductile iron, and other ferrous and non-ferrous alloys.
Shell Mold Castings
Shell mold casting is a casting process that uses a shell made of sand and resin to create parts. This process involves creating a pattern of the part, coating the pattern with a resin, and then placing the pattern in a sand mold. The mold is then heated to cure the resin, which creates a shell. Molten metal is then poured into the shell, which solidifies and is removed from the mold. Shell mold casting is known for its ability to produce precision castings with a high degree of dimensional accuracy and surface finish. It is commonly used with aluminum, zinc, magnesium, and brass alloys.
In conclusion, aerospace castings are an important component of the aerospace industry. There are several types of aerospace castings, each with its own unique characteristics and applications. Investment casting, sand casting, permanent mold casting, and shell mold casting are some of the most commonly used processes. These processes are used to create parts with tight tolerances, complex geometries, and fine surface finishes.
Materials Used in Aerospace Casting
Aerospace castings are known for their high quality and reliability, which is why they are the preferred choice for critical aerospace applications. The materials used in aerospace casting must meet strict design and construction standards to ensure their functionality, reliability, and safety. In this section, we will discuss the most commonly used materials in aerospace casting.
Aluminum Alloys
Aluminum alloys are widely used in aerospace casting due to their lightweight and high strength-to-weight ratio. They are also known for their excellent corrosion resistance and good heat conductivity. The most commonly used aluminum alloys in aerospace casting are 7075, 6061, 6063, 2024, and 5052. These alloys are heat-treated to enhance their mechanical properties, such as strength and hardness. They are also finished with a surface treatment to improve their corrosion resistance and appearance. The tolerances for aluminum alloys in aerospace casting are typically tight to ensure their dimensional accuracy.
Stainless Steel
Stainless steel is another popular material used in aerospace casting due to its high strength, toughness, and corrosion resistance. It is commonly used in applications that require high-temperature resistance and good wear resistance. Stainless steel is heat-treated to improve its mechanical properties and finished with a surface treatment to enhance its corrosion resistance and appearance. The tolerances for stainless steel in aerospace casting are typically tight to ensure its dimensional accuracy.
Copper and Copper Alloys
Copper and copper alloys are used in aerospace casting due to their excellent electrical conductivity and thermal conductivity. They are commonly used in applications that require good corrosion resistance and high-temperature resistance. Copper alloys, such as beryllium copper, are also known for their high strength and wear resistance. Copper and copper alloys are finished with a surface treatment to enhance their corrosion resistance and appearance. The tolerances for copper and copper alloys in aerospace casting are typically tight to ensure their dimensional accuracy.
Carbon and Alloy Steel
Carbon and alloy steel are used in aerospace casting due to their high strength, toughness, and wear resistance. They are commonly used in applications that require good fatigue resistance and high-temperature resistance. Carbon and alloy steel are heat-treated to improve their mechanical properties and finished with a surface treatment to enhance their corrosion resistance and appearance. The tolerances for carbon and alloy steel in aerospace casting are typically tight to ensure their dimensional accuracy.
In conclusion, aerospace casting requires materials that meet strict design and construction standards to ensure their functionality, reliability, and safety. The most commonly used materials in aerospace casting are aluminum alloys, stainless steel, copper and copper alloys, and carbon and alloy steel. These materials are heat-treated, finished with a surface treatment, and have tight tolerances to ensure their dimensional accuracy.
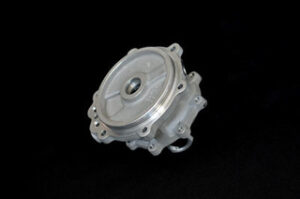
Aerospace Casting Process
Aerospace casting process involves the production of complex components and structures using various casting techniques. The process begins with the creation of a wax pattern, which is then coated with a ceramic shell to create a mold. Once the mold is created, it is heated to remove the wax and harden the ceramic shell. The molten metal is then poured into the mold, which solidifies and takes the shape of the mold.
CNC Machining
After the casting process is complete, the components are subjected to various machining operations to achieve the desired shape and size. CNC machining is a precision machining process that involves the use of computer-controlled machines to produce complex shapes and features with high accuracy.
Non-Destructive Testing
Non-destructive testing (NDT) is an essential part of the aerospace casting process. It involves the use of various techniques to inspect the components for defects and ensure that they meet the required quality standards. NDT testing techniques include X-ray inspection, ultrasonic testing, magnetic particle inspection, and dye penetrant inspection.
Heat Treating
Heat treating is a critical process in the aerospace casting process that involves the use of heat to modify the properties of the metal. Ferrous alloys and non-ferrous alloys are subjected to different heat treatment processes to achieve the desired properties such as strength, hardness, and ductility.
Coating and Painting
Coating and painting are essential steps in the aerospace casting process that help to protect the components from corrosion and wear. E-coat and powder coat are common coating techniques used in the aerospace industry to provide a durable and protective coating.
Machining Operations
Machining operations such as broaching and laser etching are used to create precise features and shapes on the surface of the components. These operations are critical in ensuring that the components meet the required specifications and function as intended.
Quality Control and Certification
Quality control and certification are essential aspects of the aerospace casting process. Barron Industries is a company that specializes in aerospace investment castings and has achieved NADCAP certification for its investment castings. Traceability and documentation are critical in ensuring that the components meet the required quality standards and are suitable for use in the aerospace industry.
In conclusion, the aerospace casting process involves various steps and techniques to produce complex components and structures with high accuracy and quality. The use of CNC machining, NDT testing, heat treating, coating and painting, machining operations, and quality control and certification are critical in ensuring that the components meet the required specifications and function as intended.
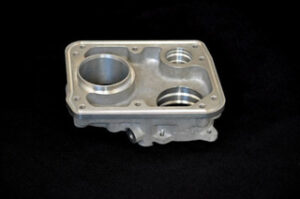
Applications of Aerospace Casting
Aerospace casting is the process of creating intricate and complex parts for aircraft, spacecraft, and other aerospace applications. It is a critical component of the aerospace industry, as it allows for the creation of parts that are both strong and lightweight.
Aircraft Components
Aerospace casting is used to create a wide variety of aircraft components, including actuator components, cargo systems, bearing cages, and hydraulic fluid system components. These components are crucial to the safe and efficient operation of aircraft, and they must be manufactured to exacting standards in order to ensure their reliability.
Aviation Industry
The aviation industry relies heavily on aerospace casting to produce high-quality parts for aircraft. Aerospace casting allows for the creation of parts that are both strong and lightweight, which is essential for the safe and efficient operation of aircraft.
Examples of Aerospace Casting Applications
One example of aerospace casting is the production of parts for the Boeing 767. The Boeing 767 is a popular commercial aircraft that requires a wide range of complex parts, including engine components, landing gear components, and more. Aerospace casting is used to create many of these parts, which are critical to the safe and efficient operation of the aircraft.
Another example of aerospace casting is the production of parts for the Apache helicopter. The Apache helicopter is a military helicopter that requires a wide range of complex parts, including rotor blades, transmission components, and more. Aerospace casting is used to create many of these parts, which are critical to the safe and efficient operation of the helicopter.
In conclusion, aerospace casting is a critical component of the aerospace industry, allowing for the creation of strong and lightweight parts for aircraft, spacecraft, and other aerospace applications. It is used to create a wide variety of components, including those used in the Boeing 767 and the Apache helicopter.
Conclusion
Aerospace casting is a crucial process in the aviation industry, and it has come a long way in recent years. The use of aerospace investment casting has allowed for more durable and affordable parts to be produced, which has significantly reduced manufacturing costs. The continuing trend in the aerospace casting community to reduce manufacturing costs means that components may be designed as investment castings capable of outstanding reliability.
The extremely high level of precision needed within the aerospace industry makes CNC machining a suitable manufacturing process for the sector. Aerospace castings tend to be the highest quality castings in the industry. Quality is driven by requirements in design, functionality, reliability, and safety. Cost is always an important factor, and cast parts must meet NASA design and construction standards: NASA-STD-6016.
In conclusion, aerospace casting is a critical process in the aviation industry. The use of investment casting has allowed for more durable and affordable parts to be produced, which has significantly reduced manufacturing costs. The industry will continue to evolve, and it is likely that new technologies will emerge to make the process even more efficient and cost-effective. As the industry continues to grow, it is essential to ensure that quality standards are maintained to ensure the safety and reliability of aircraft parts.
Aerospace industry require high precision, high durability parts, investment casting is the right process for such parts, also our heat treatment will also help to improve the properties of products.Thus to ensure the saftey and longer the serving life.
Typical aerospace investment castings are:
- Hydraulic fluid system components
- Interior components
- Landing and braking components
- Exterior and interior sensors, motion control and actuation systems
- Flight critical and safety components
- Bearing cages
- Cargo Systems
CNC Turning | Φ0.5 – Φ300 * 750 mm,+/-0.005 mm |
---|---|
CNC Milling | 510 * 1020 * 500 mm(max),+/-0.01 mm |
CNC Stamping | 1000 * 1000 mm(max),+/-0.05 mm |
Drawing Format | Auto CAD, Solid works, Pro/E, PDF.UG |
Test Equipment | D measurement instrument, Projector, CMM, Altimeter, Micrometer, Thread Gages, Calipers, Pin Gauge etc. |
We can produce a wide variety of complex aerospace casting components. Thin-walled machining is one of our core competencies. We produce parts in exotic metals including inconel, titanium and haste Alloy.